The lubrication system of a marine propeller plays a key role in reducing friction, preventing corrosion, and ensuring smooth propulsion. Regular maintenance includes checking oil quality, inspecting stern tube seals, monitoring system pressure, and preventing water contamination. Common issues such as oil leakage, overheating, and misalignment can be prevented through proactive inspections and timely repairs. Proper lubrication system management enhances vessel efficiency, reduces operational costs, and prolongs the lifespan of propulsion components.
Importance of Propeller Lubrication
A well-functioning lubrication system plays a vital role in:
- Reducing friction and wear between rotating components such as the tail shaft, bearings, and seals.
- Preventing corrosion by forming a protective barrier against seawater exposure.
- Dissipating heat, ensuring that mechanical parts do not overheat under high loads.
- Enhancing efficiency by minimizing energy loss due to mechanical resistance.
- The lubrication system is especially critical in stern tube bearings, shaft seals, and gear connections in controllable-pitch propeller ( CPP ) systems.

Key Components of a Propeller Lubrication System
The lubrication system in a marine propeller setup consists of several essential components:
- Stern Tube Bearings: Support the tail shaft and require continuous lubrication to reduce wear.
- Stern Tube Seals: Prevent oil leakage and seawater intrusion, often requiring proper lubrication for effective sealing.
- Tail Shaft: Transmits power from the engine to the propeller, necessitating smooth lubrication to prevent overheating.
- Oil Circulation System: Ensures a consistent flow of lubricant to all critical areas, usually featuring pumps, filters, and reservoirs.
- Hydraulic Couplings (in CPP Systems): Require lubrication to ensure smooth pitch adjustment without excessive friction.

Maintenance and Inspection Best Practices
Regular maintenance and inspection of the lubrication system are essential for preventing failures and ensuring long-term operational reliability. Here are the recommended best practices:
Routine Lubricant Monitoring and Replacement
- Check lubricant quality periodically using viscosity and contamination tests. Dirty or degraded oil can cause excessive wear and loss of lubrication efficiency.
- Follow manufacturer-recommended oil change intervals to maintain optimal performance.
- Use high-quality marine lubricants that meet industry standards for viscosity, anti-corrosion properties, and thermal stability.
Inspecting Stern Tube Seals and Bearings
- Check for oil leaks around stern tube seals, which could indicate seal failure or excessive wear.
- Monitor shaft alignment, as misalignment can lead to increased friction and lubrication inefficiency.
- Replace worn bearings if excessive vibration or abnormal noise is detected.
Ensuring Proper Lubrication System Pressure and Flow
- Inspect oil pumps and filters to ensure consistent oil circulation and prevent blockages.
- Monitor oil pressure gauges to detect any irregularities that could indicate leakage or pump failure.
- Flush the system periodically to remove any accumulated debris or contaminants.
Detecting and Preventing Water Contamination
- Conduct water ingress tests regularly, as water contamination can severely degrade lubricant performance and accelerate corrosion.
- Install water separation filters to remove moisture from the lubrication system.
- Check for seal integrity, as damaged seals are a common source of water intrusion.
Common Issues and Troubleshooting
Marine propeller lubrication systems are exposed to harsh conditions, leading to potential issues such as:
Problem | Possible Causes | Solution |
---|---|---|
Oil Leakage | Worn-out stern tube seals, loose connections | Replace seals, tighten fittings |
Increased Friction | Low oil levels, poor-quality lubricant | Refill with proper lubricant, replace oil |
Water Contamination | Seal failure, improper maintenance | Check seals, use water-removal systems |
Overheating | Inadequate lubrication, clogged oil circulation | Inspect oil pumps, clean filters |
Unusual Vibrations | Shaft misalignment, bearing wear | Check alignment, replace bearings if needed |
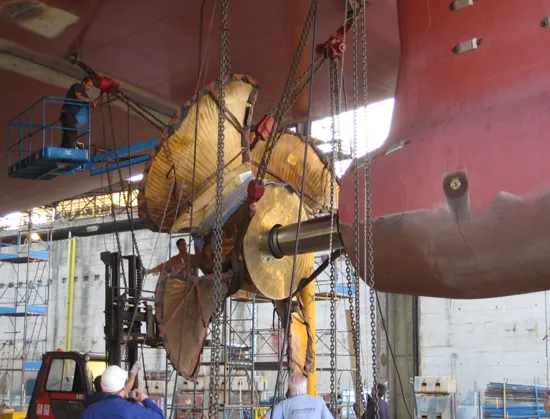
Conclusion
Maintaining a marine propeller’s lubrication system is vital for efficient and reliable vessel operation. Regular oil monitoring, proper seal inspections, and preventative maintenance ensure smooth performance, minimize mechanical wear, and extend the service life of critical propulsion components. By implementing these best practices, ship operators can reduce downtime, improve fuel efficiency, and prevent costly repairs.
